INDUSTRY STANDARD
Understanding the chemistry of fire retardants
By Edward Goldberg
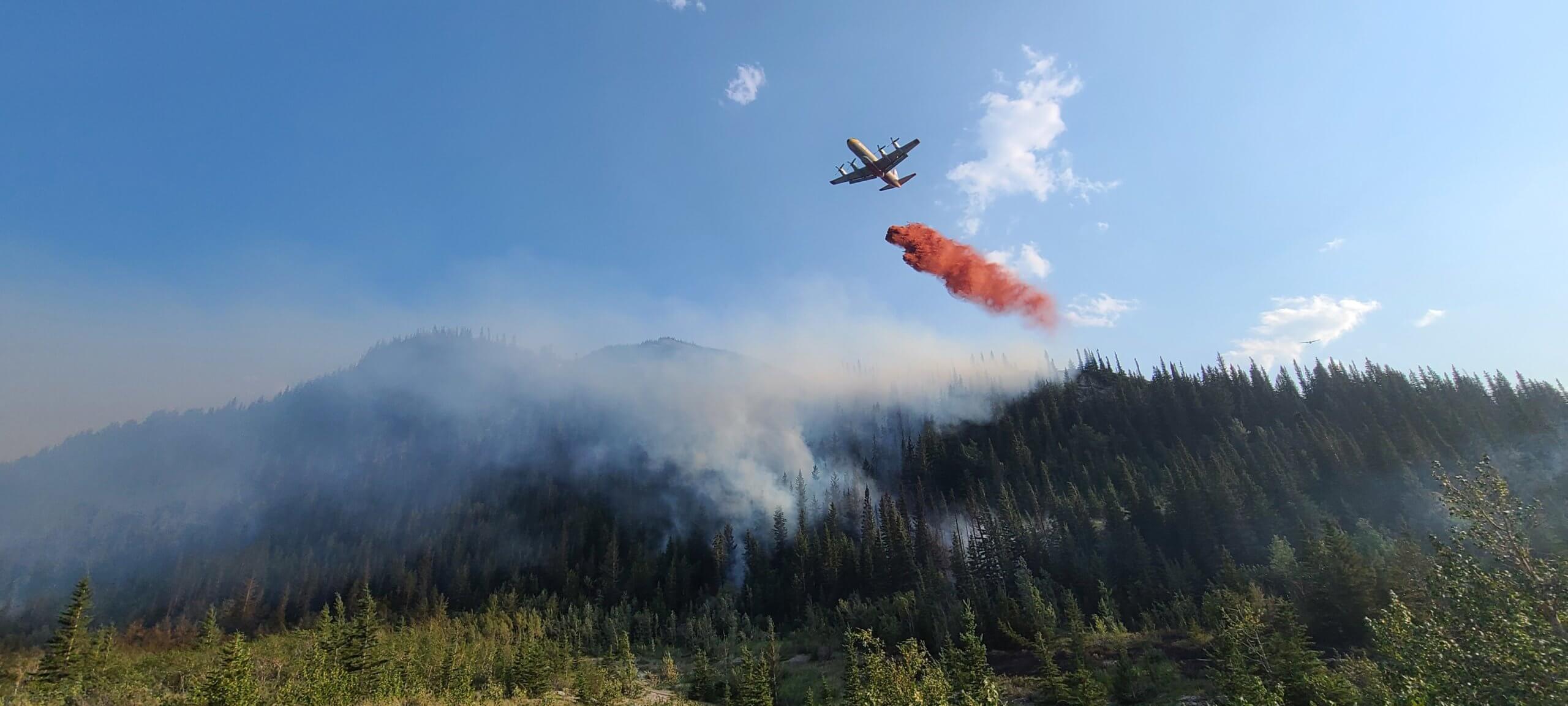
Following a study in 1954 dubbed Operation Firestop, phosphate-based retardants became the industry standard and still are today.
Photo by Ang Beaulac.
Wildfire season is getting longer, and fires are growing in intensity. This is apparent to people in the Western United States, Australia, Canada, Europe, and other parts of the world where wildfire activity has increased in recent years. As this is the new reality, it is more important than ever that firefighters and fire management agencies are equipped with the tools they need to effectively manage these fires. These tools must be safe, effective, and reliable.
LONG-TERM FIRE RETARDANT
Aerial firefighting was first attempted in the 1920s. Containers of water were literally dropped from planes on active wildfires, but this practice presented dangers to firefighters on the ground. Despite these challenges, fire-management organizations saw promise in aerial firefighting and started more sophisticated attempts in the early 1940s. These efforts were rudimentary compared to today, as very small planes were used, with water serving as the extinguishing agent. It wasn’t long before people realized that dropping water from the air to fight fires was incredibly inefficient, as the speed of the plane, combined wind velocity, and the heat from the flames would prevent most of the water from reaching the ground. Chemicals were quickly added to water to thicken it and to improve its stability and effectiveness in dousing fires.
By the 1950s, agencies started using air tankers with installed tanks to drop long-term fire retardants. Long-term retardants chemically render fuel non-flammable – a chemical reaction that does not rely on water for effectiveness. Though water is incorporated with long-term retardants, it functions merely as a tool to get the retardant to the ground. Once the retardant is on the ground, the water evaporates, leaving the retardant to function. Long-term retardant is typically used to create a fire break but is also effective for direct attack; it will remain effective for weeks or months – until a heavy rain washes it away – and it has become the dominant technology in aerial wildfire fighting.
Early forms of long-term fire retardant were developed using hydrating clays, such as bentonite and borate, and then gum-thickened waters, which are very similar to the gels that are used today. Borate was used in retardants for only a couple of years because it was found to be toxic to soil. Other chemicals were tried as potential replacements, including sodium silicate, magnesium chloride, ammonium sulfate, ammonium phosphate, and others.
This wide use of chemicals piqued the interest of researchers who wanted to understand the effectiveness of these chemicals in stopping fires. One of the first major studies to investigate this took place in 1954 and was dubbed Operation Firestop, which was a collaboration among the United States Forest Service (USFS), CalFire, Los Angeles County, the City of Los Angeles, the U.S. Department of Defense and other organizations. The major focus of the research was to study new technologies. Among the methods tested were aerial water bombing and sprays from both airplanes and helicopters, aerial backfiring from predetermined control lines, the use of fog and smoke barriers to slow fire spread, the use of backfires to turn or slow down running fire fronts, and fire-retardant chemicals and sprays.
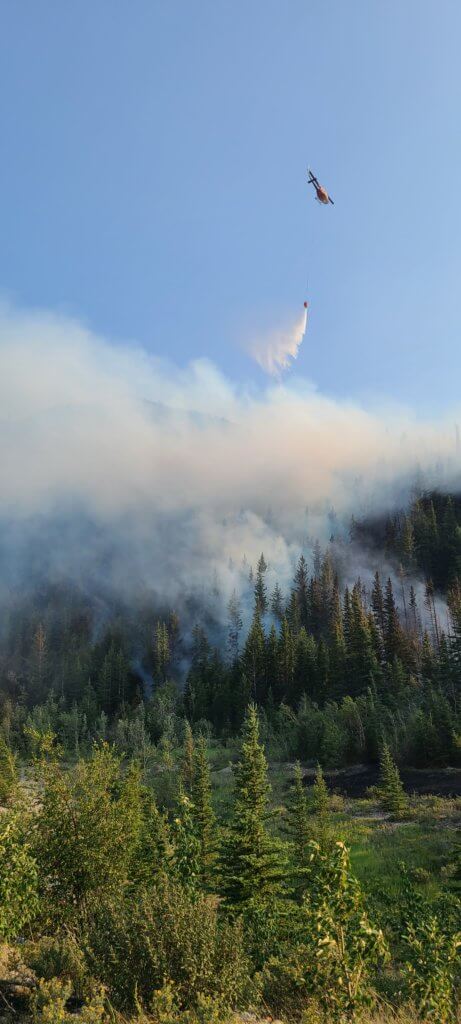
Photo by Ang Beaulac.
One phase of Operation Firestop tested the effect of fire-retardant chemicals on the ignition time of wood, on the fire intensity of burning wood, and the retardant’s ability to suppress flaming wood. The study covered several chemicals that had been in use over the previous decades in firefighting products. The findings from Operation Firestop were clear, and they have shaped the future of the retardant industry. Ammonium phosphate was among the most effective chemicals in reducing fire intensity, while boric acid, magnesium chloride, and polyvinyl acetate were among the worst. Following this groundbreaking study, phosphate-based retardants became the industry standard (and still are), while boric acid, magnesium chloride, and polyvinyl acetate were discarded and are no longer considered viable options as active ingredients for long-term retardants.
Later, in 1970, University of Montana scientist Aylmer Blakely conducted his own research and presented a paper entitled A Laboratory Method for Evaluating Forest Fire Retardant Chemicals. He built on what was found in Operation Firestop and looked at additional chemicals and effectiveness parameters. Blakely used a method called the superiority factor method, a composite of various factors combined to determine the overall effectiveness of different chemicals.
These parameters included:
- The rate of weight loss
- The remaining residue after burning
- Amount of heat radiation emitted.
Using the Blakely superiority factor, it was determined that any long-term fire retardant that measured greater than 0.3 on the scale was most effective; those that rated between 0.2 and 0.3 were moderately effective; and chemicals that scored between 0.1 and 0.2 were slightly effective. Blakely concluded (again) that ammonium phosphates topped the list of effective retardant chemicals (diammonium phosphates finished at the top, monoammonium phosphates ranked second). Potassium chloride was the least effective (finishing 14 out of 14 chemicals tested) and magnesium chloride finished ninth, failing to register any score above 0.3 in the tested superiority factors.
CONTINUOUS INNOVATION
It takes more than just the active ingredient to formulate a usable long-term fire retardant. To be effective, retardants must:
- Be safe for people, animals, fish, and the environment
- Cause minimal corrosion to protect aircraft and other equipment
- Have higher recovery rates – meaning a high percentage of the solution hits its target
- Be stable
- Be able to be stored for extended periods
- Be visible when dropped and remain visible for pilots when it is on the ground, to form a continuous fire line.
Innovations have been made to ammonium phosphate-based retardants over the last 60 years to improve these retardant characteristics. Better thickeners were developed to improve drop characteristics, more sophisticated corrosion inhibitors were added, enhanced flow conditioners made mixing easier and more efficient, and new colorants enhanced visibility and its environmental profile.
In 1975, the first fugitive color retardants started being used. Iron oxide was initially used to provide red color to the solution, but when applied it permanently stained surfaces that it contacted, including homes and other structures. This important innovation with fugitive color provided fire-management agencies the ability to effectively fight fires in aesthetically sensitive areas such as national parks and in wildland-urban interface areas, where iron oxide-colored retardants were less desirable or unacceptable. Fugitive-colored retardants also reduced the risk of staining airport runways, taxiways, and other exposed areas, as the color goes away after exposure to weather and other conditions.
In 1985, a synergistic blend of ammonium sulfate and ammonium phosphates was created to significantly reduce the cost of retardant while providing similar performance.
Advanced gum-thickened retardants were also developed, offering a range of viscosities. Previously, the only options for the fire manager were very low-viscosity (un-thickened-water-like) or high-viscosity retardants. This innovation allows the agencies using the retardant to optimize its characteristics based on the delivery system, topographical, fuel, and specific fire situation.
Today, phosphate-based retardants continue to be recognized by the scientific community as the most effective wildland fire retardants; they offer significantly higher recovery rates than water or retardants based on other chemical solutions. The water generated by fuel decomposition in the presence of the retardant adds to the efficacy of fire suppression, and it is better at preventing re-ignitions because it renders fuel non-flammable.
As a 20-year veteran of the fire safety industry, it is disheartening to see that despite all the research supporting the use of ammonium phosphate as the most effective active ingredient for fire retardants, and the continued advancements being made with long-term fire retardant, that fringe players in the industry are introducing new long-term retardant products that promote the use of chemicals that have already been proven to be detrimental and ineffective. What is worse is the fact that there are false performance claims being made and inaccurate information being spread to disparage ammonium phosphate-based retardants. If these deceptive comments are taken at face value and adopted as reality, the impact on fire fighting and people’s safety could be devastating.
THE TAKEAWAY
When considering a retardant product, determine if that product is on the USFS Qualified Products List (QPL). Long-term fire retardants included on the QPL are the only retardants that can be used on federal lands in the United States. Before being added to the list, the USFS evaluates and approves retardants using its Wildland Fire Chemicals Test Procedures (WFCS). USFS conducts a risk assessment, tests for mammalian and fish toxicity, determines whether the components present a risk to humans, and reviews the chemical makeup of the product and test its effectiveness. With the QPL designation, users can have confidence that the product is effective and safe. Many companies make product claims regarding the safety of their product, its environmental friendliness, and its overall effectiveness, but if it is not on the QPL, you have no idea what the product’s capabilities are, or how dangerous it could be.
The QPL process, based on the USDA Forest Service Specification 5100-304d, however, needs to be updated. As the agency considers new or alternate chemistries, those chemistries need thorough study – study beyond what is considered in the specification. In addition, the specification does not address mixtures of different retardant products. Mixing, in airtankers, is inevitable if multiple products are used in the field. This represents a potentially significant safety hazard as interactions between chemicals could result in dangers to life, airplanes, and the environment.
The retardant industry needs innovation. We need to keep moving forward to find new technologies to do our jobs better, to provide firefighters with new tools, to keep people safer, and to do a better job of preventing and fighting these fires. But, this has to be done in a thoughtful way that ensures there aren’t unintended consequences. Retardant is being dropped out of planes on wildlands, people, and animals, and we need to fully understand the effects, the hazards, and how it should be used. We know the capabilities of phosphate-based retardants, their performance, and how they should be used. Testing has proven its effectiveness, and that is why phosphate-based retardants are included on the US Forest Service QPL.
ABOUT THE AUTHOR
Edward Goldberg is CEO, Perimeter Solutions, a producer of firefighting products and lubricant additives.